Understanding the Working Principle of an MQS–9B Series Microswitch
To comprehend the working principle of an MQS-9B Series microswitch, it’s essential to first understand its components and construction. An MQS-9B Series microswitch consists of three main parts: an actuator, a spring, and a set of contacts. The actuator, which is usually a lever or button, is the part that comes into contact with an external force or object. The spring is responsible for providing the necessary force to return the actuator to its original position once the external force is removed. The contacts, which are made of conductive material, are responsible for establishing or interrupting the flow of electricity.
When the actuator of an MQS-9B Series microswitch is in its resting position, the contacts are typically in a closed state, allowing the flow of electricity. However, when an external force is applied to the actuator, it moves in the opposite direction, causing the contacts to open. This movement happens almost instantaneously, thanks to the snap-action mechanism employed by MQS-9B Series microswitches. Once the external force is removed, the spring quickly returns the actuator to its resting position, causing the contacts to close again.
The snap-action mechanism of MQS-9B Series microswitches is what sets them apart from other types of switches. This mechanism ensures that the contacts transition between the open and closed states rapidly, minimizing the risk of arcing or sparking and providing a reliable and consistent electrical connection.
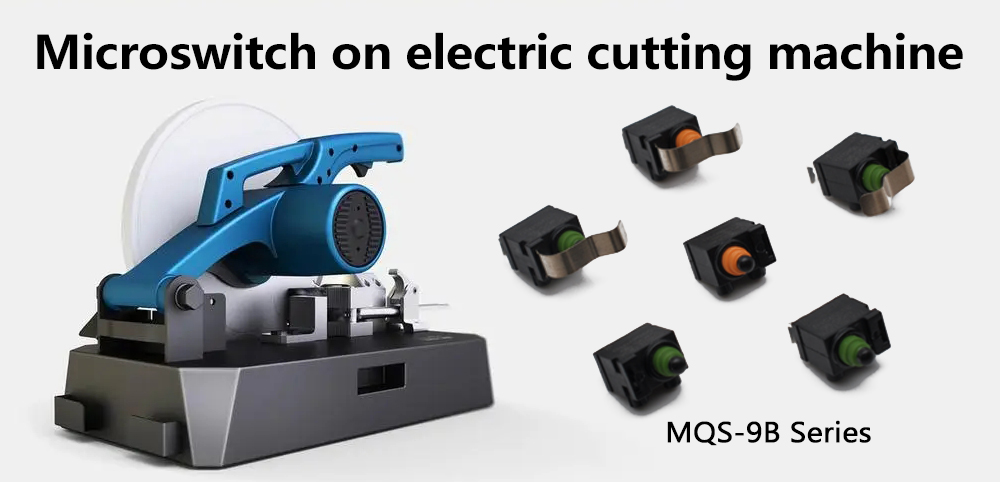
Importance of MQS-9B Series Microswitches in Electric Cutting Machines
MQS-9B Series Microswitches play a vital role in the operation of electric cutting machines. These machines are used in various industries, such as metalworking, woodworking, and textile manufacturing, to precisely cut materials into desired shapes and sizes. The accuracy and safety of the cutting process heavily depend on the proper functioning of microswitches.
One of the key functions of microswitches in electric cutting machines is material detection. These machines often need to identify the presence or absence of materials before initiating the cutting process. Microswitches are used to detect the material’s position, ensuring that the cutting blade only activates when the material is in the correct position. This feature helps prevent accidental cuts and damage to the machine or the material being cut.
Moreover, microswitches are also used for safety purposes in electric cutting machines. They are installed in various parts of the machine to ensure that certain conditions are met before the cutting process can commence. For example, microswitches can be used to detect if the machine’s safety cover is closed properly or if the emergency stop button has been pressed. By incorporating microswitches in these safety mechanisms, electric cutting machines can prevent accidents and protect both the operator and the machine.
How Does a MQS-9B Series Microswitch Work in an Electric Cutting Machine?
Now that we have a good understanding of the working principle and components of microswitches, let’s explore how they function in an electric cutting machine. The specific placement and function of microswitches may vary depending on the design and model of the machine, but their overall purpose remains the same – to ensure precision and safety during the cutting process.
In an electric cutting machine, microswitches are strategically positioned to detect the presence or absence of materials. When the material is properly positioned, the microswitch is activated, allowing the cutting process to begin. On the other hand, if the material is not in the correct position, the microswitch remains deactivated, preventing the cutting process from starting.
For example, imagine a scenario where an electric cutting machine is used to cut sheets of metal. Microswitches can be placed at the edges of the cutting area to detect the presence of metal sheets. When a sheet is correctly aligned with the cutting blade, the microswitch is triggered, signaling the machine to initiate the cutting process. If the sheet is not properly aligned or is missing, the microswitch remains inactive, preventing the machine from cutting.
This material detection feature provided by microswitches ensures that electric cutting machines only operate when all the necessary conditions are met, minimizing errors and optimizing productivity. Additionally, it adds an extra layer of safety by preventing the machine from cutting if an object or a person is in an unsafe position.
Common Applications of MQS-9B Series Microswitches in Electric Cutting Machines
Microswitches find a wide range of applications in electric cutting machines due to their versatility and reliability. Here are some common uses of microswitches in these machines:
1. Material detection
MQS-9B Series Microswitches are used to detect the presence or absence of materials, ensuring accurate cutting and preventing damage to the machine or the material.
2. Safety mechanisms
MQS-9B Series Microswitches are incorporated into safety mechanisms such as emergency stop buttons and safety covers to prevent accidents and injuries.
3. Positioning control
MQS-9B Series Microswitches can be used to control the positioning of cutting blades or other moving parts, ensuring precise and consistent cuts.
4. Limit switches
MQS-9B Series Microswitches are often used as limit switches to define the limits of movement for certain parts of the cutting machine, preventing overextension or collisions.
5. Machine status indicators
MQS-9B Series Microswitches can be used to indicate the status of the machine, such as whether it is in operation or if there is a malfunction.